European Salt Batteries
- h2worlddaa
- Mar 30
- 6 min read
Updated: Apr 2
Sodium-ion batteries (SIBs) are emerging as a sustainable and affordable alternative to lithium-ion batteries. After years of research and development, they have the opportunity to unlock the batteries for the future of energy storage.
A Brief History of Sodium Ion Batteries
Sodium-ion batteries (SIBs) represent a promising alternative to lithium-ion batteries (LIBs);
Sodium ion is a good candidate for energy storage for several reasons. Sodium is much cheaper and 1000 times more abundant on Earth than lithium, and available cathodes also use Earth-abundant materials, avoiding the supply chain risks of nickel and cobalt in lithium-ion batteries. Sodium ion chemistry is based on intercalation just like sodium-ion batteries; sodium ions travel back and forth between the anode and cathode carrying charge and energy. The similarity to sodium-ion batteries in mechanics, performance, and manufacturing has enabled simplified knowledge transfer and accelerated development and commercialization. Current Sodium-ion batteries have a lower energy density than lithium-ion batteries, making them a strong candidate for large-scale stationary energy storage systems.
Both lithium-ion and sodium-ion cathodes were discovered around the same time. However, sodium-ion research was hampered by the lack of a suitable intercalation anode. Around 2000, the discovery of hard carbon (HC) as an anode material sparked renewed interest in SIBs. The 2010s saw rapid growth, most likely due to the push for alternatives to LIBs, resulting in the development of new cathode materials, complete cell assembly, and several startups focused on commercialization. The first cylindrical 18650 SIBs were assembled in 2015 with a Na3V2(PO4)2F3 (NVPF) cathode and an HC anode through the collaboration of several institutions within the French Network for Electrochemical Storage (R2SE). Commercialization efforts resulted in 1-5 Ah pouch cells from Faradion, the first company to commercialize SIBs; a declaration of 10,000 SIBs produced by Tiamat, the startup spun out of R2SE; and the announcement of a 100 kWh battery installation for energy arbitrage by Chinese company HiNa. Physics-based modeling can play a unique and important role in the ongoing development of SIBs.
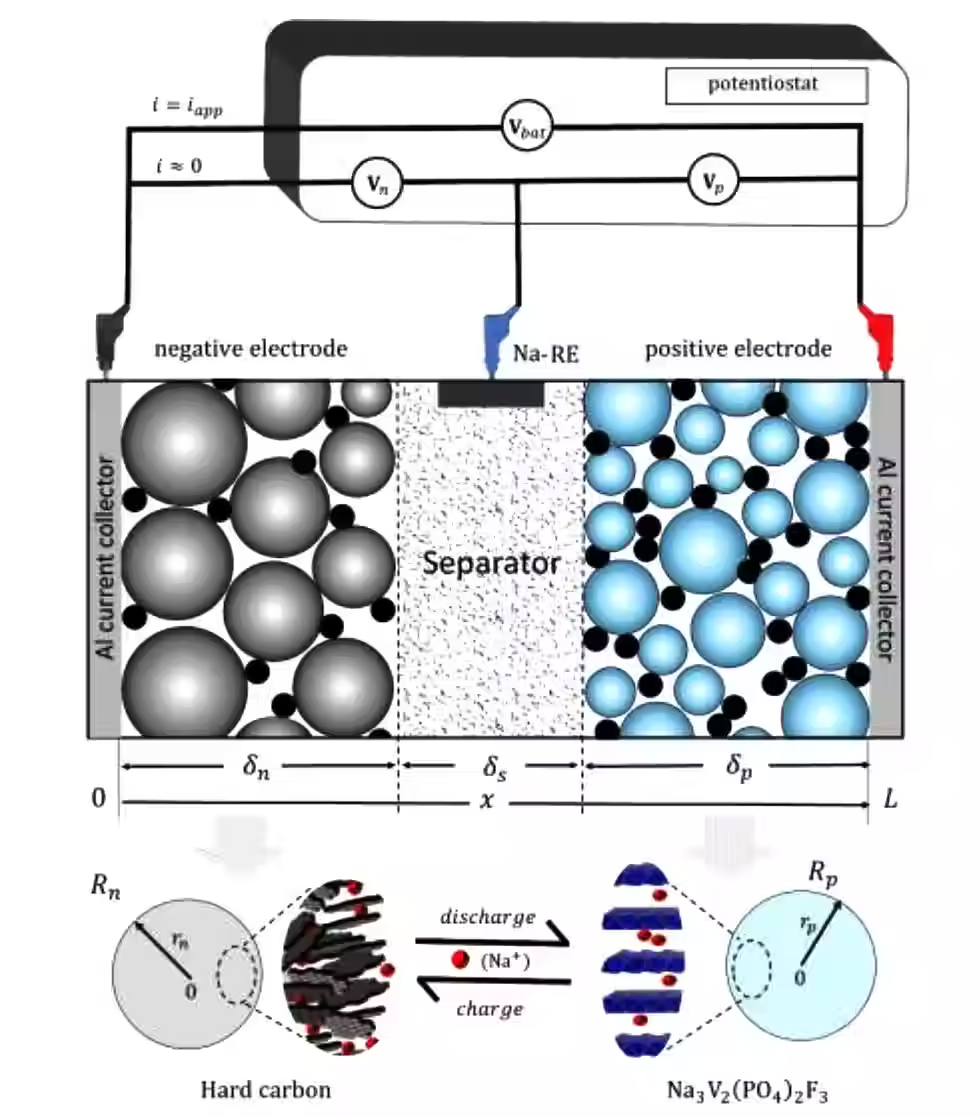
The first physics-based pseudo-two-dimensional (P2D) model for sodium-ion batteries was published in 2022 by Chayambuka et. al. The model uses the generalized framework of the Doyle-Fuller-Newman P2D model for lithium-ion batteries, which predicts the performance and dynamics of intercalation batteries. The modeling work was coupled with experiments on a sodium battery with a cathode consisting of NVPF particles, an HC anode, and a 1 M NaPF6 EC 0.5 : PC0.5 (w/w) electrolyte. The reaction for NVPF is
Na3VIII2(PO4)2 <--> F3 NaVIV2 (PO4)2F3 + 2Na+ + 2e−
where 2 Na+ are transferred per unit of NVPF, resulting in a capacity of 128 mAh/g. HC is a non-graphitic carbon with a complex structure: they have graphene-like layers within an amorphous microporous phase. Charge transfer occurs via adsorption on graphene layers and filling of meso- and nanopores. There are multiple proposed mechanisms for HC, which may depend on the precursor and structural properties, and this remains an active area of research. The specific capacity of HC is around 300 mAh/g, similar to that of graphite in LIBs.
Model parameterization can be difficult and complex, but remains a key component of ensuring accurate battery models. To create an experimentally predictive set of basic parameters, the authors of the SIB P2D model used experimental techniques and parameter estimates on GITT and cyclic half- and whole-cell data, as well as electrolyte measurements and statistical mechanics simulations for transport properties. The schematic for the sodium-ion battery can be found in the figure above, taken directly from their work. A 3-electrode setup with a Na-ion reference electrode was used to measure individual electrode voltages, and the model output was optimized on that rather than the total battery voltage to minimize error. The relevant parameters and process details can be found in their experimental and modeling papers (refs. 1 and 2).
This work highlights the power of appropriately parameterized physics-based models; model predictions for velocities from 0.1C to 1.4C were less than 2% error from experimental curves and less than 50 mV absolute error. The authors found that contact resistance becomes important at higher velocities for accurate predictions. Additionally, high-speed performance was hampered by poor mass transport in both the electrodes and electrolyte. The results suggest that reducing particle size in the HC electrode will improve high-speed performance while diffusion within the NVPF particles was found to limit mass transport.
The figure below reproduces the C-rate study by Chayambuka et al. The
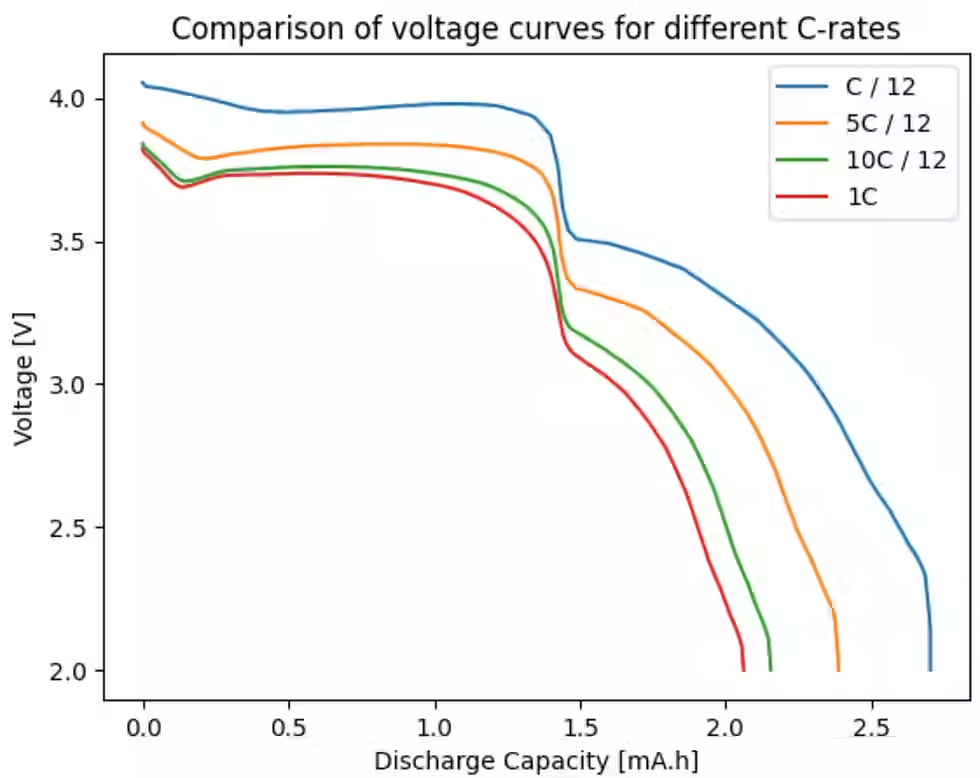
The sodium-ion battery landscape is rapidly evolving as leading companies innovate to meet the growing demand for sustainable energy solutions. This development is in response to the growing need for alternatives to traditional lithium-ion batteries. By 2033, the global sodium-ion battery market is expected to grow from $438 million in 2024 to over $2 billion, growing at a compound annual growth rate of 21.68%. Here are the top sodium-ion battery companies in 2025:
Altris AB
Sweden’s Altris AB has introduced a commercial-size sodium-ion battery cell that offers energy density comparable to LFP lithium-ion batteries. By partnering with Clarios for low-voltage automotive applications and Polarium for energy storage, Altris AB is pioneering practical adaptations to sodium-ion.
As the sodium-ion battery market evolves, these six companies are leading the charge with breakthrough innovations and partnerships. Their technologies promise to provide sustainable energy solutions, paving the way for a future less dependent on lithium-ion batteries.
TIAMAT , based in France, develops sodium-ion batteries suitable for mobility and stationary energy storage. Their batteries have attracted attention for their ability to charge in just five minutes and for their high safety standards. TIAMAT recently secured €30 million to establish a factory capable of producing 5 GWh of sodium-ion batteries per year in France.
Northvolt is making waves with a sodium-ion battery that exceeds an energy density of 160 Wh/kg. This Swedish company makes batteries without relying on critical metals. Instead, it uses abundant, low-cost materials, making its solutions both affordable and sustainable.
Faradion Limited, a British company, specializes in non-aqueous sodium ion battery technology. These batteries are designed for high power applications such as electric vehicles and grid storage. Faradion products are distinguished by their long life and ability to operate over a wide temperature range.
Small pilot plants and large projects
Currently, mostly pilot plants are in operation and a few smaller factories are starting up, producing only a few gigawatt hours (GWh) of sodium-ion batteries per year, but the capacities publicly announced by various raw material and battery manufacturers amount to well over 100 GWh by 2030. Significantly more capacity than has been financed so far could be developed by 2025 if investors are found during 2024. The prediction of a radical conversion of a large part of the industry to a new technology in a few years may seem bold, but in the last five years alone, this has happened twice in the battery industry with NMC811 and LFP. Sodium-ion barely requires a new plant technology, only different starting materials and production parameters.
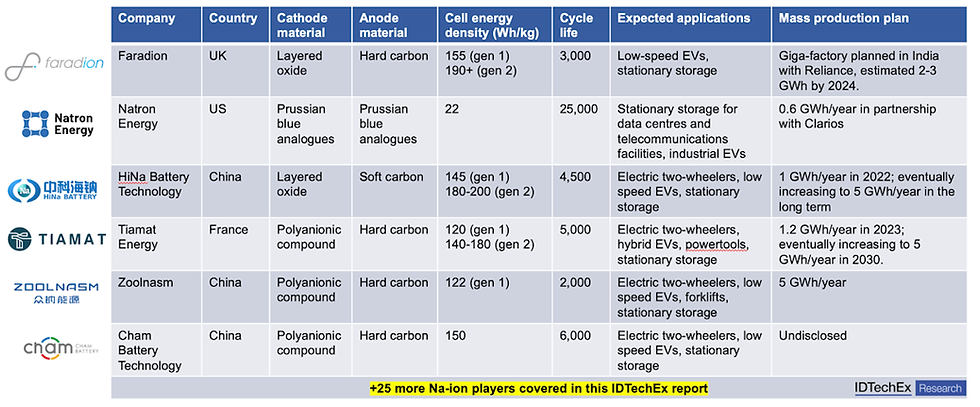
Significant savings compared to LFP are initially unlikely
There is currently no cost-effective battery technology with an energy density between lead-acid and lithium-ion batteries. According to IDTechEx research, the average cost of sodium-ion battery cells is $87/kWh, taking into account different chemistries. By the end of the decade, the cost of manufacturing sodium-ion battery cells using primarily iron and manganese will likely bottom out at around $40/kWh, which would be around $50/kWh at the pack level. Sodium-ion cells are likely to initially command a premium, but IDTechEx expects the cost/price to decline in the short term through manufacturing efficiencies, scale, and technology development. However, long-term cost reductions become more difficult as the technology and manufacturing become more established and mature.
Sodium is not the end of lithium
For most electric vehicles, volumetric energy density is the first or second priority because the more space a battery cell takes up for a given energy density, the fewer cells you can fit under a vehicle, limiting range. For grid storage, the space taken up by battery packs does not affect their commercial viability and the priority is the cost per kWh per cycle. Commercial energy storage is about controlling costs and this is where sodium ion can potentially dominate other chemistries. The greatest potential in transportation applications for sodium ion batteries exists wherever the energy density of lithium batteries is not fully utilized. This includes almost all electric cars with a so-called standard range, i.e. a reduced battery capacity compared to more expensive models of the same construction. There, sodium batteries with faster charging rates and lower capacity loss at low temperatures could be a very attractive alternative. Above all, with this alternative energy storage technology, lithium batteries will be available where they are truly indispensable.

Comments